Not Your Parents Basement Wall System
May 27, 2013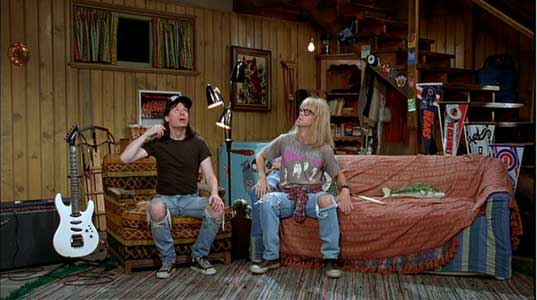
Basement wall system technology has come a long way from the days of our parents and grandparents. We all remember the basement wall system of the past, install some wood stud framing in front of the concrete basement wall and cover it with some beautiful wood paneling from your local lumber yard.
At the time this was a revolutionary way for DIY homeowners and contractors to finish basements. The wood paneling had some very attractive qualities: it was more resilient to water and mold than plaster or sheetrock; it was easier and faster to install; it required much less maintenance; and it was a very cost effective solution to providing more living space on a tight budget.
As time passed and paneling became dated decor, more and more homeowners turned to the widely used conventional construction products of the late 80’s & 90’s: 2×4 wood framing, fiberglass insulation and sheetrock which became the industry standard for finishing a basement.
There were certainly improvements built into the basement wall system during this time. The use of pressure treated lumber for any locations where wood framing came in contact with the concrete basement wall or floor, helping to provide protection against wood rot from moisture being released by the concrete. The application of coatings and paints to the concrete basement wall helped reduce moisture levels behind the basement wall system. All of these steps made it clear that contractors and homeowners were starting to realize that the basement environment could not be utilized as a solid canvas for finishing without adding some type of protection against moisture, the critical ingredient for mold growth.
Maybe this shift in thinking was brought on by memories of wonderful holiday gatherings at Grandma and Grandpa’s house when they were kids and forced into that “musty smelling” paneled basement to play board games with the cousins. A generation of homeowners forever traumatized to the idea of ever having a finished basement. Maybe the shift was brought on by the ever so publicized “sick building syndrome”. In 1984, the WHO (World Health Organization) released a report stating 30% of all buildings maybe suffering from symptoms of SBS (Sick Building Syndrome) thus raising our awareness of the importance of indoor air quality.
The advancements in building science and more specifically IAQ (Indoor Air Quality) have also helped to raise the level of services provided by professional contractors through education and training. Most likely the combination of these events along with many other factors from our daily lives have lead us to a solid and clear understanding that the basement environment is unique and must be treated as such. When you combine this thinking with advancements in construction products and you have the basement wall system of today.
In 1998 Owens-Corning launched one of the first products sold as a complete basement wall system. The fiberglass panel was heavily promoted, distributed and installed only through franchises across the country. It wasn’t the best looking basement wall system and certainly didn’t look like the rest of the house.
The panel had ugly seams where the panels met, only came in one color which you couldn’t paint and was very flimsy. It did however deliver one major benefit over conventional building products, it had almost no organic materials, the breeding ground for mold in a basement environment. As with most innovations made in free markets, competitors have improved upon the Owens-Corning product and todays panel is light years ahead of the Owens-Corning panel manufactured in 1998.
Today’s basement wall system panels are seamless, paintable and manufactured with Magnesium Oxide (MgO) skins over a Expanded Polystyrene (EPS) core. The EPS core provides an R-Value of 18, meeting or in most cases exceeding local building codes for a basement wall. The MgO skins provide a strong durable shell that outperforms standard sheetrock or drywall, especially in the basement. These basement wall system panels allow you to frame, insulate and sheetrock all in one step. Best of all, these panels provide you with the look, feel and comfort you expect in your home.
Make sure to install the right basement wall system for your basement finishing project and avoid having your Parent’s basement.